NHQA: A Quality Award for Home Builders in North America
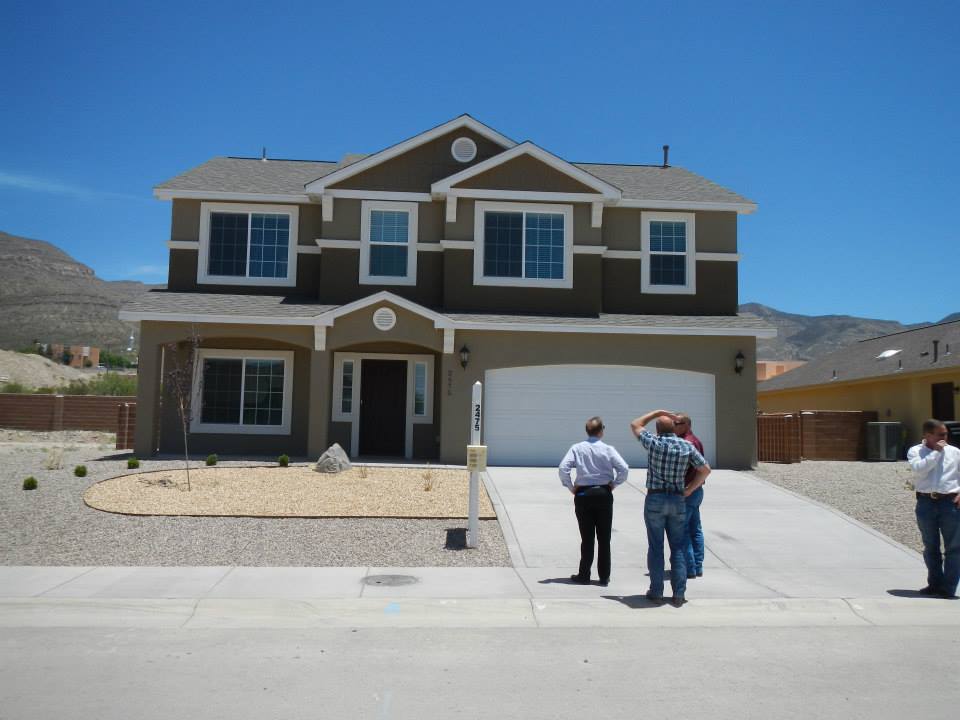
There is nothing more rewarding for a company or organization than a industry recognised award for quality and excellence.
Of course, it’s all about profitability and repeating business but there is nothing more satisfying for a business owner in construction industry than getting recognised for driving excellence in every aspect of their business.
There is no doubt, it can finally make all the difference on winning new jobs and projects (like the existence of an ISO Certificate may do).
We had the opportunity to discuss with Denis Leonard PhD ASQ Fellow regarding one of the most important Quality Awards for construction industry in the United States: the National Housing Quality Award (NHQA).
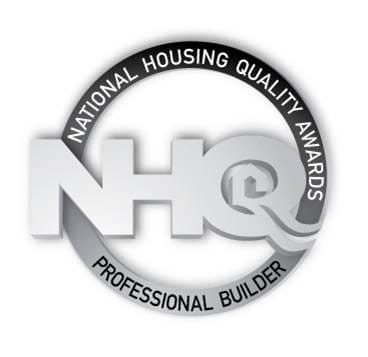
So, what is the National Housing Quality Award (NHQA)?
The NHQ (National Housing Quality) Award was launched in 1992 and is dedicated to the advancement and recognition of organizational excellence in homebuilding in North America.
It is based on the US Malcolm Baldrige Criteria for Performance Excellence and National Quality Award that was launched in 1987 and is now used by 43 State Quality Award Programs and by 60 countries and inspired the launch of the European Quality Award.
The NHQ Award was initiated to assist those in the home-building industry improve every aspect of their business. It is based on a set of criteria to assess the organizational performance of builders.
The criteria consist of eight sections: Leadership, Strategic Planning, Process Management, Customer Satisfaction, Human Resources, Construction Quality, Trade Relationship and Business Results. The eight criteria provide a tool to evaluate an organization and identify strengths, as well as opportunities for improvement.
The criteria consider:
- Importance of leadership
- Need to consider all elements of an organization
- Strategic importance of scanning and analyzing the business environment
- Value of creating focus on customers and employees
- Emphasis of identifying and monitoring key performance indicators and
- Methods of approach and deployment for improvement action plans
It also drives the need to:
- Align resources
- Improve communication
- Increase productivity
- Boost effectiveness
- Achieve strategic goals
Who supports and funds the NHQ Award?
Professional Builder Magazine sponsors the Award program. The program judges each volunteer their time and are responsible for all their personal travel and miscellaneous expenses. Most are previous NHQ Award winners others are quality and industry experts, each having witnessed the impact that this program has had on their own business performance, have elected to support the NHQ Award program and give back to the industry.
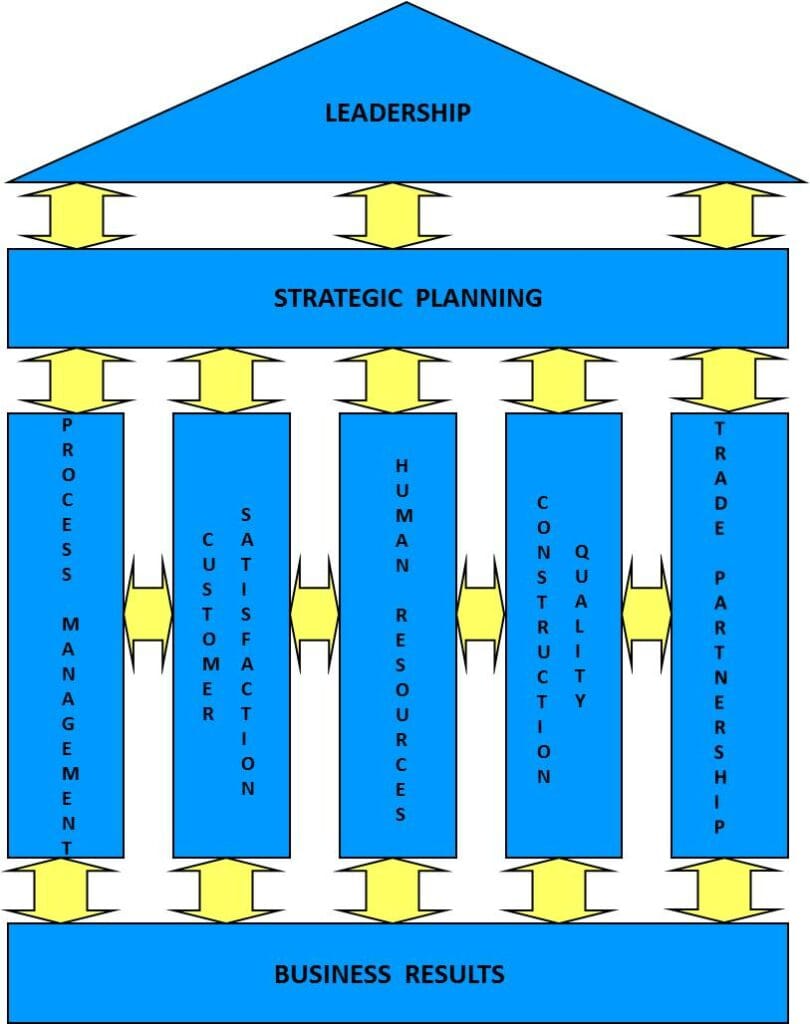
Why should a contractor/builder apply for the Award? Can someone outside of the US still apply?
Currently any builder in North America can apply, that means any builder in Canada, USA or Mexico!
To quote a recent winner:
This is the best and most honest consulting an [organization] can get to improve their company.
The program will help to improve the performance of your business and dramatically impact your bottom-line. The process of applying for the NHQ Award, and gaining the detailed feedback report from industry experts, can provide fast-track opportunities for improvement and help to reduce costs, defects, cycle times and improve customer, employee and trade partner satisfaction.
Who can apply for the Award? Is it only for Residential contractors (Home Builders) or any Civil Engineering contractor can actually apply?
The NHQA process is designed for Residential Home Building Contractors.
Home Builders of all sizes apply.Previous recipients have had as few as 15 employees, or up to several thousand; built 15 homes per year, or as many as 20,000. Many have been involved with entry level homes under $150,000, while others have dealt with homes in excess of $1 million.
Regardless of how small or how large, production homes or custom, the NHQ Award is relevant to everyone and has provided measurable improvement for all that have taken the steps to apply. Some apply to benchmark themselves against the best in the industry, most apply with a strong desire to improve their company.
Over 60 companies have earned an NHQ Award; many have achieved recognition at one level and then reapplied to move to a higher level. Some have even returned years later to ensure that they continue to meet changing industry benchmarks and challenge themselves and earn the “Gold” again!
NHQA builders are using quality management tools and techniques to drive performance improvement to survive and thrive. In the profiles of each builder you will see them leveraging process mapping, DMAIC improvement teams, employee recognition, net promoter scores, balanced scorecards and kaizen lean events. They have a strong focus on strategic planning, employee empowerment, trade relationships and of course the customer.

What is the relationship between the NHQA and the ISO:9001 standard? Are there any similarities in the approach? Does the NHQA refer to the standard and if so, how?
The NHQA is not prescriptive, it does not advocate any particular tool or technique. It’s more about using the tools, techniques etc that work for your organization to address the issues at hand.
However, using a Quality Management System (QMS) or the ISO9001 standard would provide a fundamental infrastructure and management system to help coordinate and manage many of the key issues at the core of the NHQA Model/Criteria to drive and function a well-run business.
What impacts have previous winners seen?
From 1993 through 2009 the following impacts were cited as direct results from the feedback to the NHQ Award application:
Profits (Gross Margins): 12-20%
Revenue: 15-100% increases per year
Construction Costs vs Budget: +/- 1%
Customer Satisfaction: 93-97%
Referral Rates: 29%
Cycle Time Reductions: 15-50%
Zero Defects at Closing: 98%
Defect Reductions: 11-75%
Employee Satisfaction: 94%
Trade Satisfaction: 95%

NHQA is more than 20 years old so there must be some pretty good statistics on where and how the applicants/contractors/builders fail significantly (design, collaboration, planning, supervision, resources etc). Would you like to share some of these information? Where does the industry fail the most?
Areas that we see as constantly needing attention include training, succession planning and trade relations.
Training, training training. Its always an issue, it involves time, money and effort but its essential. The key we have found is ensuring that the correct training is provided, that is, that employees are not just ‘given any training to fulfil an agreed number of hours each year’. Rather what is needed is training that addresses strategic and operational gaps in the organization and the specific developmental needs of an employee.
The majority of home building companies are small family owned businesses. Few engage in detailed, formal, written succession planning. Yet this is critical. Those that do succession planning tend to do it in a very informal way and only address the top 1-2 people in the company. However, if succession planning is done correctly it uncovers the development that is needed and the on the job training and mentoring to develop future leaders.
It may seem that as sub-contractors are actually doing the work and are therefore essential, that there would be very close working relationships between the main contractor/home builder and the subs. But in so many cases this is not the situation.
While a focus on the customer is a key element of Quality, so is a focus on the Employee AND so is the Trade Partner/Sub Contractor/Supplier relationship!
NHQA builders use annual conferences, satisfaction surveys, working teams to focus on improvement projects, creating and updating Scopes of Work, having weekly meetings to review schedules, safety, environmental issues, quarterly Councils to forge strong and detailed working relationships. (The Councils are where the leaders of the key trades and the builder owners meet to discuss strategic long term issues.)

As we are entering the BIM era (…or just thinking of how to enter it) do you think that new technologies like BIM, cloud collaboration tools and integrated electronic management systems would actually change the way builders operate and do business? Or this is pure science fiction for smaller companies who may not have the resources to invest on such tools?
Technology is becoming cheaper, easier to use and so more and more accessible to builders even the small builders.
But what we have seen is that technology is not a silver bullet, if the underlying processes are poor and technology is seen as a silver bullet to solve the problems it can result in a ‘poor process made faster’ and not necessarily better.
The basics are the basics. If process improvement and a strong customer focus are used to drive the business and appropriate technology used sensibly and integrated into how the business functions then yes BIM, Cloud collaboration tools etc can make a business faster, more efficient and effective and NHQA Recipients have leveraged these technologies to improve their business and improve the experience for the customer who more and more are tech savvy.
Thanks very much!
My Comment:
This is a great initiative that targets the SMEs in construction industry in North America. Though it’s not directly related to ISO standards or relevant compliance, it does provide a benchmark for all these small companies and it’s actually giving them the opportunity to strive for continuous improvement . It’d be good to see something similar in Europe, Australia or elsewhere.
Member discussion